Casting Aluminum 101: Vital Actions for Newbies
Casting Aluminum 101: Vital Actions for Newbies
Blog Article
Light Weight Aluminum Casting Solutions Introduced: Important Insights and Tips
Checking out the realm of light weight aluminum spreading solutions can unveil a world of complex procedures and nuanced factors to consider that are critical for effective end results. As industries progressively turn to light weight aluminum for its lightweight yet long lasting properties, comprehending the basics of casting comes to be critical. From the basic methods to the intricate information that can make or break a casting job, there is a riches of insights and tips waiting to be discovered. As we venture into the realm of aluminum casting services, prepare to reveal the vital aspects that can shape the trajectory of your projects and boost your understanding of this detailed craft.
The Basics of Aluminum Casting
What basic procedures are included in aluminum casting that create the backbone of this widely used production technique? Light weight aluminum spreading is a cost-efficient and functional technique made use of in numerous industries to develop complex and complex steel elements. The process begins with the melting of light weight aluminum ingots in a heater, typically at temperatures ranging from 1220 ° F to 1670 ° F, depending on the certain aluminum alloy being used. Once molten, the aluminum is poured right into a pre-designed mold tooth cavity, where it strengthens and takes the form of the mold.
Trick aspects such as mold design, gating system, and cooling down rate play a vital function in identifying the last high quality of the actors aluminum part. The mold and mildew can be made of numerous products like steel, sand, or investment casting wax, relying on the complexity of the part and the desired surface area coating. After solidification, the mold is eliminated, and the spreading goes through completing procedures such as warm therapy, machining, and surface layer to meet the required specifications. Recognizing these fundamental procedures is important for accomplishing top notch light weight aluminum spreadings with mechanical homes and precise measurements.
Various Casting Approaches Clarified
Checking out the numerous strategies employed in light weight aluminum spreading offers useful understandings into the varied approaches used to achieve elaborate and specific steel components. One common technique is sand casting, where a mold is developed utilizing compacted sand around a pattern of the wanted part. This strategy is cost-effective and flexible, suitable for both easy and complicated shapes. Another approach, die spreading, entails injecting molten aluminum into a steel mold under high pressure. Die casting allows high accuracy and repeatability, making it optimal for automation of tiny to medium-sized parts. For even more intricate designs, investment casting is frequently favored. This technique utilizes wax patterns that are disappeared, leaving a cavity for the molten light weight aluminum to load. Investment spreading returns precise information and smooth surfaces, making it popular in markets such as aerospace and automotive. Each casting approach has its unique advantages and is picked based upon factors such as expense, intricacy, and quantity factors to consider.
Aspects to Consider When Choosing a copyright
When selecting an aluminum spreading solution company, reviewing their experience and knowledge is critical for ensuring top quality and dependability in the production procedure. The copyright's experience in the field indicates their familiarity with various spreading strategies, possible obstacles, and finest practices. It is necessary to ask about the types of projects they have actually worked on in the past, ensuring they align with the complexity and specifications of your own project.
Furthermore, consider the service provider's credibility within the industry. Search for testimonials, endorsements, and study that show their capability to deliver high-grade aluminum castings constantly. A reputable copyright will certainly typically have certifications or affiliations with industry companies, showcasing their dedication to excellence and adherence to sector standards.
In addition, examine the copyright's capabilities in regards to customization, quantity demands, and job timelines. Guarantee that they can fit your specific demands and have the versatility to range production as required. Reliable interaction and transparency pertaining to prices, preparation, and quality assurance procedures are also crucial factors to take into consideration when selecting an aluminum spreading company.
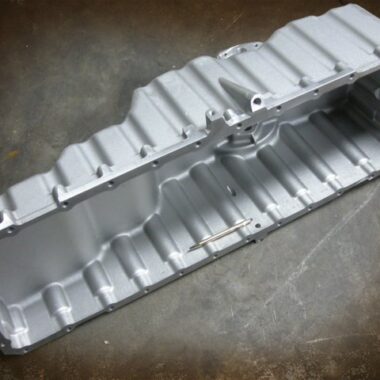
Common Obstacles and Solutions
Navigating with the complexities of aluminum spreading processes typically offers manufacturers with a collection of challenges that need innovative solutions to make sure performance and quality in production. One typical obstacle faced in aluminum casting is the formation of problems such as porosity, shrinkage, or additions because of incorrect mold and mildew layout or inadequate metal quality. These flaws can compromise the architectural honesty of the end product. To address this, makers must carry out detailed simulations and examinations to optimize the casting process criteria and make certain the top quality of the molds and products made use of.
One more obstacle depends on attaining precise dimensional accuracy, specifically for intricate geometries. Variations you could check here in cooling rates, mold development, and material properties can cause inconsistencies from the designated measurements. Executing advanced website here innovations like computer-aided design (CAD) and computer system numerical control (CNC) machining can enhance precision and uniformity in light weight aluminum spreading. In addition, preserving appropriate control over the melting and putting processes is crucial to prevent problems like getting too hot or uneven circulation of the liquified steel - casting aluminum. By investing in automation and real-time tracking systems, makers can improve procedure control and reduce variations, ultimately enhancing the overall top quality of light weight aluminum cast items.
Tips for Optimizing Your Spreading Projects
By making sure that the gating system is well-designed and correctly put, you can improve the circulation of liquified aluminum and reduce the opportunities of issues in the final spreading. Furthermore, using computer system simulations can assist in predicting and assessing the circulation of steel throughout the spreading process, permitting for adjustments to be made prior to real manufacturing begins.
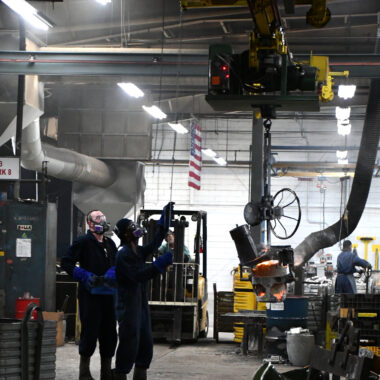
Final Thought
Finally, comprehending the basics of aluminum casting, different casting methods, aspects to take into consideration when picking a copyright, usual obstacles and services, and pointers for optimizing casting projects are essential for effective end results. By adhering to these insights and applying ideal companies, people and practices can guarantee effective and reliable light weight aluminum spreading solutions that meet their particular needs and demands.
Comprehending these essential procedures is essential for attaining top quality aluminum castings with accurate dimensions and mechanical residential properties.
When choosing an aluminum spreading solution supplier, reviewing their experience and competence is vital for making sure top quality and reliability in the production procedure. Reliable interaction and openness relating to prices, lead times, and quality control procedures are also vital aspects to take into consideration when picking an aluminum casting solution copyright.
Navigating through the intricacies of light weight aluminum spreading procedures typically presents manufacturers with a series of difficulties that need cutting-edge services to make sure effectiveness and quality check this in manufacturing. One typical challenge encountered in light weight aluminum casting is the formation of issues such as porosity, contraction, or additions due to improper mold and mildew design or poor steel quality.
Report this page